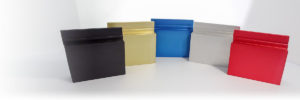
© 2025 AMF Technologies, Inc. All rights reserved.
By visiting our site, you agree to our privacy policy regarding cookies, tracking statistics, etc.
Plating steel, copper, and brass to close tolerances is our specialty. Whether the work is a Military specification or a customer-driven specification, we handle the job expertly, professionally and to the quality standard you demand. With over 40 years of experience the utmost attention to detail and commitment to quality, our team has the expertise to finish your parts to exact specification. Tight tolerance jobs are completed right the first time.
Different finishing processes are used to achieve different results but there are typically additional considerations.
Turnaround time is often a concern. Some metal finishing options take longer than others, so production speed is a factor if when you need to meet tight deadlines. The hardness of the substrate may come into play. A milder process may fall short of achieving the desired result on harder metals and an aggressive process may damage parts made of softer materials. Cost is often a key point. Evaluating alternative processes may help save your company money. In some instances, you may be able to achieve comparable results using a process that has a lower cost.
Not all metal finishing options are ideal for every project. We provide personalized advice when you need it. Contact us for advice or a custom quote.
Sulfamate Nickel – QQ-N-290 Class 2
Sulfamate nickel is an electrolytic plating process that protects against corrosion and an economical restoration to original specifications. Because the coating is 99.9% pure nickel, it is incredibly dense and exceptionally corrosion resistant. It also increases wear resistance, tensile strength, and temperature resistance.
Bright Nickel -QQ-N-290 Class 1
Bright nickel plating can be used to coat various metal substrates including brass, copper alloys, steel, and other metal to provide a clean bright decorative finish. The bright reflective finish is a result of its elevated sulfur content. Bright nickel offers good corrosion resistance and increases surface hardness and conductivity.
Electropolish – ASTM B-912
Electropolishing removes imperfections and contaminants from metal surfaces using a combination of chemicals and electrical current. The process is similar to passivation with the use of a chemical bath to remove surface contaminants and protect against corrosion. Electropolishing goes a step further by using an electrical current that removes microscopic surface layers of material to achieve a smooth finish. It removes as little as .0001″ up to .0015″ (per surface) to produce the desired result.
Electroless Nickel – MIL- C-26074
The MIL-C-26074 electroless nickel plating specification is used for applying precision coatings. It is a common specification used in the aerospace, automotive, electronics, and pharmaceutical industries. Electroless Nickel is the coating used for the most challenging applications. With its consistent chemistry, electroless nickel can uniformly coat parts of varied sizes and the most complex shapes. It contributes corrosion and wear resistance properties for metals surfaces such as steel, copper, and brass.
Zinc – QQ-Z-325B Type I, II, III
Zinc plating provides excellent corrosion resistance. It prevents corrosion by forming a barrier serving as a sacrificial anode to protect metal cathode substrate. The protective barrier inhibits rust by preventing moisture from reaching the part beneath. Zinc-coated steel offers additional benefits that include lightweight, strength, ductility, low cost, and recycling.
Black Oxide – MIL-C-13924B
Black oxide is a finish that provides a combination of characteristics that cannot be accomplished in other ways. It is a conversion coating produced by a chemical reaction with the metal to form a finish which is integral to the part’s surface. Black oxide is abrasion resistant but primarily used for its aesthetic properties. Alone it provides moderate corrosion resistance and is parts typically receive a supplementary treatment of oil or wax for added protection.
© 2025 AMF Technologies, Inc. All rights reserved.